The Central Part of KAHL Recycling Plants:
High-performance presses of KAHL
For decades, KAHL pelleting plants have been applied successfully for compacting organic products of different particle sizes, moisture contents and bulk densities. The products are pressed through a die by pan grinder rollers, formed into endless strands, and then cut to the desired particle length by means of knives.
We develop our machines constantly with regard to performance and efficiency. KAHL presses are particularly appropriate for the processing of products, which are difficult to pellet.
Waste tyre recycling plants and moulding plants
Waste tyres consist of caoutchouc, textile fibres, steel and additives, and have a high recycling potential.
For more than 20 years, Amandus Kahl has been active in waste tyre treatment and has delivered plants from the reception to the production of new products from waste tyre crumb worldwide.
The latest enhancement of the technology is the processing of tyre crumb to finished products to increase the value of the crumb. Amandus Kahl offers automated, modular moulding plants for the production of mats, profiles and mouldings. Through the use of changeable moulds, these systems can produce a variety of products in the fields of fall protection, sports, construction and transport.
KAHL Wood Pelleting Plants
Amandus Kahl offer pelleting presses with a drive power from 3 kW to 500 kW. In total, 12 different sizes are available. The production capacities of most plants range between 1.5 and 8 t/h per press.
Smaller plants work efficiently, too. Larger plants of up to 40 t/h are provided for industrial production of pellets.
Pelleting Plants for Domestic and Industrial Waste
Modern waste management means to minimize or even better prevent the production of waste in the community.
The central part of the processing plant is the flat die press. By means of the flat die press, the waste materials are more or less strongly compacted depending on the quality requirements. At the same time, the light fractions with a high calorific value in particular are homogenized.
The slightly compacted or slightly pelleted material is also called fluff. The pelleting elements such as pan grinder rollers (A) and die (B) exert a combined shearing and cutting impact on the product to be processed.
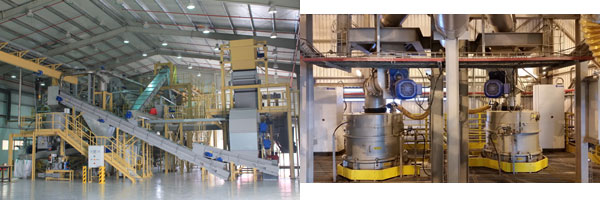