Mrs. Nikolova, what made you participate in the international forum “NO accidents?
Out of doubt, that what made us to take the decision to participate in the forum is the need of the Bulgarian market of an event from this kind on a local territory and of course the fact that we have the exact solutions, which a subject of the forum. There are several forums and conferences in Europe addressed to this type of industrial issues but however those events are taking part abroad and not each one Bulgarian company is having the chance and the ability to visit them. Our company policy is in every way to familiarize our clients with technological innovations - by organizing individual seminars, information about international events or by participating in forums of this kind. Taken together, all these factors tipped the balance in favor of the "to participate" almost instantly.
What solutions and innovations will you present and in which areas they apply?
Within the forum we will present two types of solutions: ultrasonic detectors and gas detectors.
The ultrasonic detectors Sonaphone from the German manufacturer Sonotec GMBH are used for preventive maintenance of machines and equipment or the so-called. Condition based maintenance. The main applications are compressed air and technical gases leak testing, tightness testing, inspection of pumps, gearboxes, valves and steam traps and electrical installations.
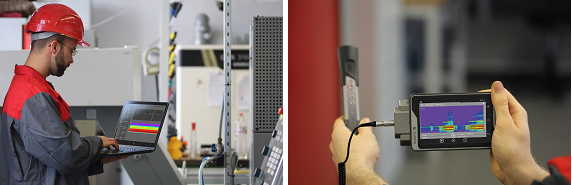
The product range of gas detectors from the Japanese manufacturer Riken Keiki Co. LTD includes personal and stationary gas detectors as well as gas leak detectors. Gas detectors use different sensors depending on their application and can be used as alarms for the detection of only one particular gas or to be able to monitor the levels of several gases simultaneously.
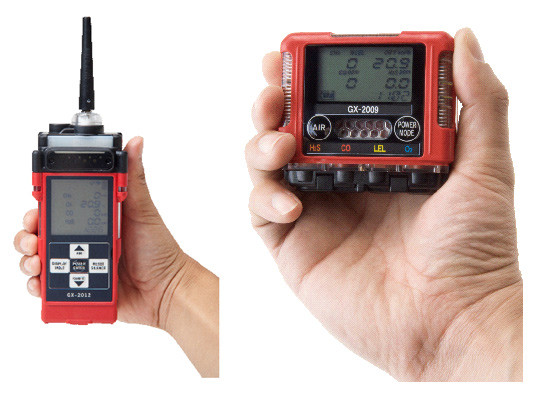
Tell us more about the benefits of putting them into practice?
The ultrasonic detectors have several applications. The detections of compressed air and technical gases leaks aims to identify and eliminate both small and large gaps in gas transmission systems. Large gaps are leading to a drop in the pressure and impede the operation of pneumatic machines. The small gaps by themselves are insignificant, but the combination of all of them is leading to a considerable load on the compressors in order to be able to provide the required pressure. The practice shows that about 30-35% of the produced compressed air is lost, mostly by such gaps. Maintenance of gearboxes, steam traps and valves provide information on the current state of the equipment. Assuming the measured results from the previous months, a tendency model concerning equipment’s condition can be made and at the earliest stage a defect can be detected i.e. a shutdown can be planned for the repair of the production facilities at the appropriate moment and to prevent accidents. The investment in these appliances has a very rapid return - depending on the size of the plant, the investment returns from 3-4 to 10-12 months.
Inspection of electrical installations (especially high-voltage ones) has always been a challenge. The reason is that in case of an accident, the destructive force is enormous. The two main problems with this type of inspection are the arcing and the electrical discharges (corona effect). The thermography is most commonly used for inspection of a corona effect, but the problem is that the corona does not exist below 1000V and does not generate heat below 24 000V. In these situations, ultrasonic detectors have no obstacles and are capable of detecting defects at a very early stage.
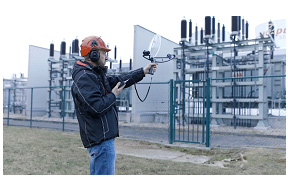
The regular inspection of valves and steam traps is essential for preventive maintenance. The early detection of steam trap leaks or fails and signs of wear leads to increased operational reliability, and considerable cost savings. The Sonaphone devices can be used for the testing of the functionality of any type of steam trap e.g. for float, thermodynamic and thermostatic traps or for valves in systems with a flow of steam. The device enables the control of the proper functionality of steam traps and also allows an estimation of any losses of steam within the system (wasted steam = wasted fuel = wasted money).
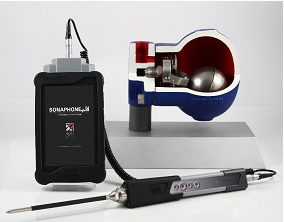
Gas detectors are primarily used for labour safety and alerting. In refineries, nuclear and thermal power plants, as well as in some industries, gases that are hazardous to human health and life are used (or waste). In these situations, on the one hand, detectors with alarm levels are installed on the premises, and on the other - employees are having personal gas detectors. The purpose is to signal as early as possible if there is an excess concentration of a gas, which is an indication of a defect in any of the systems. Some detectors can also be used to find leaks and then to repair the system.
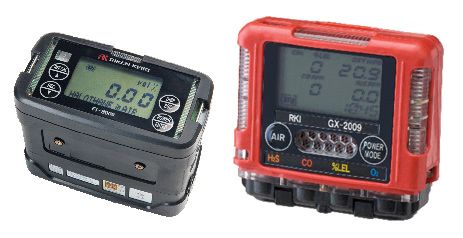
It is important to note that personal gas detectors save lives in such situations - in addition to signaling elevated values, medical teams subsequently have information on the amount of the absorbed toxic gases.
The gas detectors are ATEX certified for use in explosive environment, which is one of the major benefits of choosing a gas detector for any production classified as explosive.
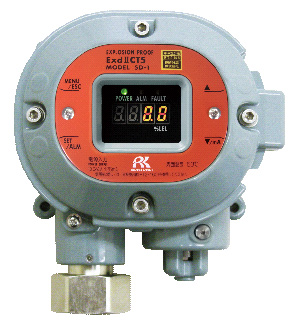
Which companies are your customers?
Our customers are enterprises of various character - in the field of energy, production of metal, plastic and glass products, processing of raw materials and go to companies that perform the control and inspection of installations and equipment.
Please share about some of your future development plans?
For the next year we have planned an expansion of the team of specialists (on all territories of the Balkans where we are active). The Balkan market is really big and we are trying to give to our customers the needed attention I terms to execute our projects on a professional level.
In terms of event participation (technology exhibitions and conferences), we have already planned to participate in more than 25 events on the Balkans. This does not include the individual seminars we organize when there is a new innovative product on the market which we want to present it to our customers as soon as possible.
In addition, we are investing more and more money into purchasing demo equipment so our customers can gain insight into new technologies and the results they can achieve with them.
More about Trokuttest Group Bulgaria
Trokuttest Group Bulgaria LTD is part of international group of companies, developing trade and consulting activities on the Balkans, which headquarter is situated in Zagreb (Croatia). The company is participating in the international forum Accidents Avoidance.
Its activity is connected with delivering of equipment and consumables for the industry – equipment for non destructive testing, mechanical testing, laboratory equipment, heat treatment etc.