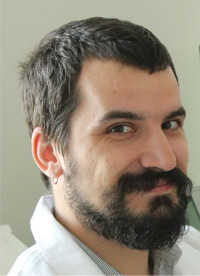
Department of Metalic Construction Materials,
Technopark Kralupy VŠCHT,Praha
Work experience
2016 – present Technopark Kralupy of University of Chemical Technology (UCT) Prague
project manager, senior researcher
Area of focus: corrosion in oil & gas, (cyclic) corrosion testing,
metallic and organic coatings, hydrogen embrittlement of advanced high-strength steels.
2014 – 2015 ÚJV Řež, a.s. (Nuclear Research Institute)
effect of irradiation on mechanical and corrosion properties of metals,
corrosion in energetics, fracture toughness
11/2009 – 9/2014 UCT Prague, PhD student, researcher
Advanced materials for heat exchangers for energy industry,
corrosion of high-alloyed creep resistant steels
Participation in 9 research activities/reports
Corrosion of piping and tanks for crude oil:
Corrosion is the fundamental damaging mechanism in crude oil piping and storage tanks. If not controlled carefully, the corrosion can result in oil spill, contamination of soil and possibly explosion. Consequently, due to natural aggressivity of crude oil, carbon steel piping needs to be replaced every decade or so.
Aim of our research was to determine the main corrosion factors. Based on the operational data , the corrosion in pipes is strongly localized, and it is accelerating in time. Based on literature review, four main corrosion mechanisms were proposed - uniform corrosion where localization is caused by other factors, truly-localized corrosion types (corrosion under deposites), corrosion caused by gasses (CO2, H2S) and microbially induced corrosion (MIC).
In experimental part, the oil-water mixture was analyzed to determine its aggressivity. The type of damage was assesed on pipe segments using visual evaluation and metallography. Chemical and phase composition of solid layers on the inner surface was studied using XRF, XRD, FTIR and ICP-EOS. Bacteria were analysed via qCPR.
It was concluded that corrosion under deposites is the key phenomenon, however other factors, such as presence of water, elevation and others also have strong effect.
Metallic alloy coatings on steel:
Zinc coatings are one of the common means of steel protection in atmospheric conditions. Performance of these coatings can be improved by alloying – addition of other elements, which improve the protection capability by different mechanisms. Zinc aluminum coatings (galfan, galvalum) have been used for several decades with good results. Modern, commercially available alloy-coatings are Zn-Mg and Zn-Al-Mg (magnelis, magizinc, ZAM etc.).
Experimental data show that the mechanism of the improved performance involves short-time protection by magnesium corrosion products which gives time for the more stable zinc and aluminum corrosion products to form. Overall improvement of corrosion rate can be up to 80 %. Nevertheless, specific issues, such as corrosion protection in crevices and delamination of paint must be considered.
Futher improvement can be found by using another alloying elements, such as Si, Cr, Mn and others. These coatings are not yet commercially available (or scarcely), since several challenges remain – mainly the productions issues related to metallurgy of this complex alloy and problems arising from precipitation of undesired phases in the microstructure.